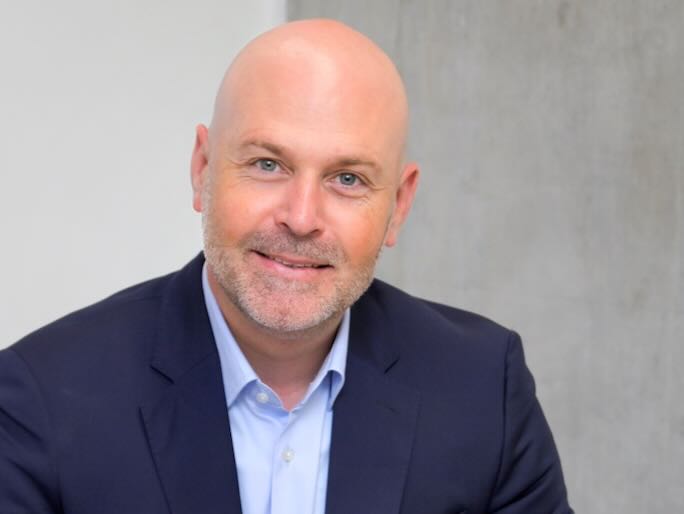
En esta tribuna, Hicham Kabbaj, director general de Dassault Systèmes para España y Portugal, explica cómo los gemelos virtuales están impulsando la transformación digital en la industria 4.0.
Hace más de 10 años, en la feria industrial Hannover Messe de Alemania, se introdujo el concepto de Industria 4.0, que marcó un antes y un después en el sector. Representó un cambio de paradigma, en el que máquinas, productos y sistemas están interconectados digitalmente, creando un entorno de comunicación y colaboración constante. Dio pasó a las fábricas inteligentes, donde los procesos se optimizan en tiempo real y los datos impulsan la toma de decisiones. Y llegando a 2024, ¿cómo se ha avanzado en esta transformación?
A pesar del inmenso potencial de la Industria 4.0, todavía existen algunos obstáculos en esta nueva etapa: muchas empresas no encuentran técnicos calificados capaces de adaptarse al entorno digital y abordar la cuarta revolución industrial.
Es aquí donde entran en juego tecnologías como los gemelos virtuales: ofrecen la posibilidad simular toda una línea de producción en un entorno virtual antes de construirla físicamente. Esto es exactamente lo que están haciendo muchos fabricantes hoy en día. No solo les permite probar diferentes configuraciones y procesos, sino que también les ayuda a reducir el tiempo de puesta en marcha y utilizar sus datos para mejorar continuamente sus operaciones.
Pensemos en ellos como una evolución de los gemelos digitales. Mientras que estos primeros se centran en un objeto específico, las experiencias de gemelos virtuales te permiten ver, modelar y simular todo un entorno complejo, impulsando la innovación en todas las etapas del ciclo de vida del producto.
Y eso no es todo. Es posible desplegar tecnologías como la inteligencia artificial y el mantenimiento predictivo avanzado para prever problemas antes de que ocurran. ¿Cómo? Monitoreando el comportamiento de los equipos y optimizando los procesos de mantenimiento y reparación. Esto no solo reduce el tiempo de inactividad, sino que también aumenta la eficiencia.
Una tecnología con beneficios tangibles
Los beneficios de los gemelos virtuales en el entorno industrial son realmente notables. Con ellos, es posible innovar de manera más rápida e inteligente que nunca.
Imagina tener un gemelo virtual hecho a medida para las necesidades de cada cliente. Por ejemplo, gracias al gemelo se crea un mantenimiento sostenible y predictivo basado en datos. Utilizando inteligencia artificial y aprendizaje automático, se analizan los datos de los sensores para detectar y corregir posibles fallos en una etapa temprana. Esto permite realizar un mantenimiento proactivo planificado para minimizar el tiempo de inactividad. Además, ofrece la capacidad integrar la tecnología de realidad aumentada para visualizar el entorno real en su totalidad mientras proyectamos información virtual adicional, como una ventana de visualización ampliada, sobre la imagen de la cámara de una tablet o smartphone. Esto facilita diagnósticos precisos y acorta los tiempos de reparación.
La optimización de procesos es otra área en la que los gemelos virtuales pueden ser de gran utilidad. Con ellos, se puede simular y probar diferentes escenarios antes de implementar cambios en la producción. Y gracias a esto, es posible optimizar los procesos, reducir costes y minimizar riesgos.
El mantenimiento predictivo también es clave para anticipar incidencias y errores. Al monitorear constantemente el gemelo virtual, se evitan posibles problemas, reduciendo el tiempo de inactividad y ganando una mayor eficiencia.
Igualmente, en el diseño y prototipado, los gemelos virtuales suponen una buenísima herramienta: facilitan el diseño y la prueba de nuevos productos y procesos antes de su producción física. Esto acelera el desarrollo y mejora la calidad, ganando una mayor ventaja competitiva en el mercado.
Además, con los gemelos virtuales, se planifican líneas de producción en 3D con anticipación. Esto asegura que las nuevas máquinas y robots móviles se ajusten al diseño y estén posicionados de manera óptima. Y, al simular flujos de trabajo para identificar errores y cuellos de botella antes de la implementación física, se ahorran tiempo y recursos.
Empoderar a la fuerza laboral del futuro
No cabe duda de que la industria 4.0 transformará la forma en la que se trabaja. Los empleos están evolucionando, y con ellos, surgen nuevos roles. Las empresas ahora necesitan personas con habilidades específicas y especializadas que puedan adaptarse rápidamente a los cambios en el sector. Por ejemplo, la capacidad de trabajar con diferentes lenguajes de programación, conocimientos prácticos en sistemas operativos y redes, habilidades de análisis de datos o programación robótica.
En mi opinión, es sumamente importante que la fuerza laboral del futuro esté capacitada y empoderada para enfrentar estos desafíos. Por eso, es crucial crear un entorno colaborativo de última generación que fomente el aprendizaje continuo y la adquisición de habilidades. Esto no solo contribuirá a la satisfacción de los empleados, sino que también aumentará su eficiencia en el trabajo.